Kaufman Implements Epicor as New ERP System
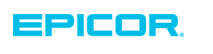
Kaufman Container is a leading packaging sourcing center in the United States. For the past 100 years, the company has provided packaging components, custom and stock molds, package development, quality assurance, and technical support to a wide range of customers and markets. Kaufman’s capabilities are endless, offering a variety of products including glass, plastic, aluminum, and metal containers, tubes, closures dispensing systems, celon bands, and more.
Prior to their Epicor implementation, Kaufman was running several non-integrated systems, and users were having to do each other’s jobs—for example, if inventory was needed for a job and one of the systems stated there was inventory on hand, there was no trust in any system of reference, and the material was manually verified to be there.
Larry Keilin, IT director, spearheaded the implementation of Epicor. “The transition from our old system to our new system was less painful than I expected—for many employees, the day you switch from an old system to a new system is the day they love the old system,” Keilin commented. “A large number of our employees got on the Epicor bandwagon and became excited about all the work they can now do that they couldn’t do before. We are truly seeing the benefits, for example for the purchasing department, the Buyers Workbench is such a useful tool that it really stands out, and our customer service department really loves the way they can take an old order, copy it, and create a new one—it’s a huge time saver for them.“
Kaufman initially implemented Epicor ERP to work as closely as possible to existing business processes, as followed with their legacy ERP. While there was a successful transition to Epicor, partnering organization Encompass Solutions identified that Epicor was not being used to its full advantage, and that there were some additional modules that would need implementation to get maximum functionality from Epicor ERP.
Kaufman contracted Encompass Solutions to perform an end-to-end business process review (BPR) to determine the best business processes to follow and unleash the maximum benefit from the newly implemented Epicor ERP product. This one-week exercise flushed out many areas for improvement, and a recommendations document and go-forward plan were implemented. Kaufman’s key goals from this BPR were to achieve better tracking of sales and gross margin data to sales persons and customers, improve inventory management, and integrate production management.
Every business area was assessed, and recommendations for change were made, particularly in the areas of engineering, production, inventory, purchasing, costing, and accounting.
Some key recommendations were to continue the implementation with some additional modules that were not included in the initial cutover—including CRM and the Epicor Configurator—as well as better implementing production and inventory management. Encompass provided a go-forward path to have everything implemented.
Other key recommendations were changes to costing to allow Kaufman to be more specific in assigning costs for production times, to leverage time-phased material requirements to drive purchasing decisions, and to expand the number of warehouses and bins used to reduce the amount of time staff spend locating inventory. A plan to move Kaufman to the scheduling engine was also produced—typically refinements over a six-month period provide an accurate, trusted model.
“Encompass has done a great job at assessing the situation, with BPR guidance to systematically attack and resolve pain points following the implementation,” concluded Keilin.